Everything That People Also Search for Custom Packaging Nowadays
2022-08-18 20:24:55
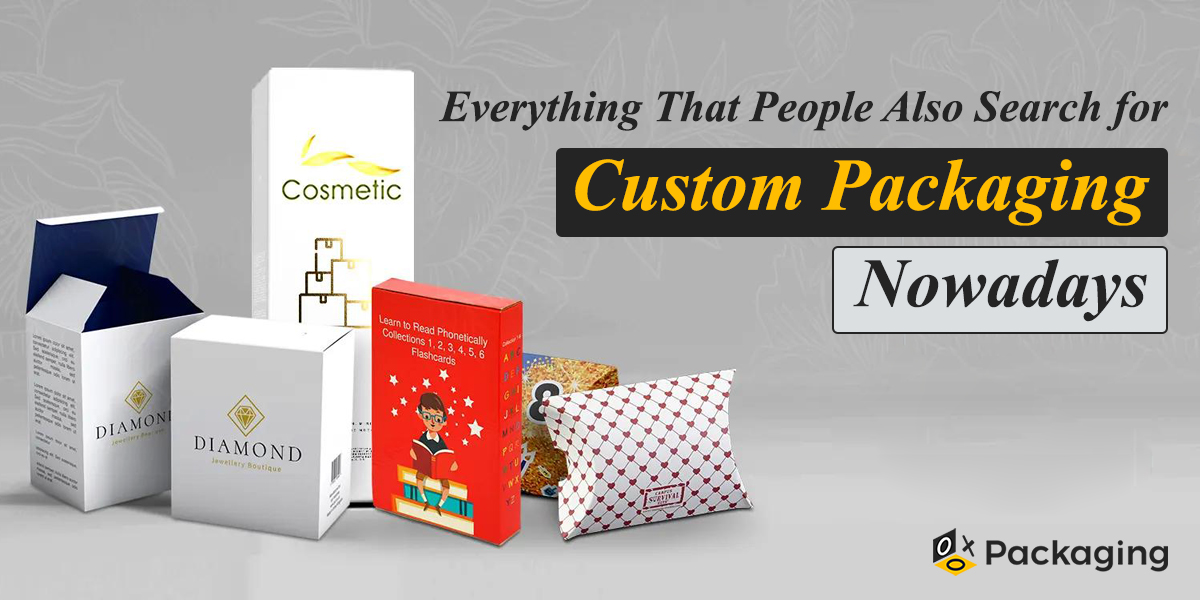
Packaging trends have changed to a large extent. There was a time when people used to search for custom packaging. This is when the representative of a packaging company was responsible for the whole product packaging. The guy used to roam the streets, visit offices and market his company.
The retail companies were used to giving their packaging orders to him. Then the guy would go back to the office and inform them about the order. Thus, production would start. Today, People also Search for Custom Packaging, but in a different way.
The subject of today is how the trends in custom paper and paperboard packaging have changed and how online merchandising has made it easy. The following contents will elaborate the revolutionary steps that have changed product packaging.
- A Brief History of Procuring the Packaging
- A Short Introduction to Packaging Materials
- Different Types of Custom Packaging
- The Importance of Product Design
- How Does Printing Play Its Part?
- How Do Paper/Paper Board Stocks Get Printed?
- The Future in Search for Custom Packaging
A Brief History of Procuring the Custom Packaging
If we go way back to the year 1817, then it was the start of product packaging. History tells us it was the year when man made the first corrugated box in England to pack a product. Our ancestors first used set-up boxes in 1839. Robert Gair was born in Scotland. He was a printer by profession. He had a great aptitude for making packaging boxes. Robert Gair accidentally came across the making of prefabricated Packaging Boxes.
We can say it was the first unassembled packaging box. We don’t have much idea about that packaging box. But the available history of that time indicates that it was a flat box. It had creases in it, and it was glued to the opposite panels. This is the same practice for us today.
I have seen a similar procedure for transporting the packaging boxes in OXO Packaging. We make the product boxes from a single piece. Then we stick their opposite ends together to keep them flat. And door-deliver to the client’s location.
-
A Short Introduction to Packaging Materials
Procedures are the same. Nowadays, people also search for custom packaging of cereals, jewelry, bakery, and sanitary products, etc. And the prefabricated way of packaging boxes introduced by Robert Gair has made it easy. If you are not making a rigid set-up box, then it is very easy to deliver conventional materials.
Rigid boxes are also known as handmade boxes. Packaging companies make them by using gray board. This is the most durable paperboard material for the retail industries. People use this material to make luxury boxes.
The other three highly usable materials are cardboard, corrugated, and Kraft. Cardboard is a coated material. It has a lush white surface. For people who are looking for packaging boxes with neat printing, cardboard is the ultimate choice for them.
Many people used to think that having a digital quality result on packaging boxes is very difficult. They thought that only digital printers could give real-life quality images. But cardboard has been very well adapted to offset machines. It is very easy for us to print the packaging products in bulk using modern printing machines.
Kraft is another choice for the people who search for custom packaging. Paper manufacturers make this material from wood pulp. It is famous as a biodegradable material. But if we talk about gray board, cardboard, or corrugated material, then these are all also fully ecological. Kraft is the most affordable of the whole lot when we look for custom packaging.
So, it is always easy to make packaging boxes for different products from these materials. Retailers frequently use them to make Custom Candle Boxes, Bath Bomb Boxes Wholesale, Custom Jewellery Boxes, Display Boxes Wholesale, Gift Boxes Australia, Pillow Boxes Wholesale, and a variety of other product boxes.
Corrugated material is mostly used to make mailer boxes. This material is also well known for making shipping boxes. It is essential to differentiate between cardboard and corrugated materials. Many people mix the specifications of cardboard and corrugated stock. They give a single name, "cardboard," to both materials. This is not right.
As mentioned above, cardboard is a coated material in white colour. However, the composition of corrugated stock is entirely different. Corrugated material has two contents. One is the wavy layer. The second is two sheets. The wavy layer is also called the flute, and it is pasted between those two sheets.
This is how paper manufacturers make a durable layer of corrugated material. Paper manufacturers make it more durable according to the requirements. If they paste multiple layers of corrugated layers over one another, the corrugated material becomes harder. If you ask an expert, this is how it becomes highly shock-proof.
And this same quality makes it the best shipping box. Its default colour is always brown. Packaging companies paste the outer layer of gloss or matte paper over it and thus make it a colourful packaging box for the retailers. This technique is ideal to make shipping boxes for the people who search for custom packaging.
-
Different Types of Custom Packaging
Not every packaging company offers the customisation for the masses who search for custom packaging. Customising the packaging products is a different sphere altogether. It requires the product to be designed from scratch. Once, I was pondering over the history of OXO Packaging and I was thinking about why they call it a one-stop packaging shop.
Then I came to know that it has a separate design department, a segregated printing press, and a split unit for pasting and shipping. If we ask an expert, then this is what people also search for custom packaging in their wishful brand. They like to have all their packaging procedures under one roof.
If we ponder over it more, we come to know that people like to get new trends in custom packaging. Experienced product designers tell us excessive use of packaging features might affect the visual appeal of product design. They say it is better for retail packaging to be simple.
"Simple" is not less. Indeed, it is the sensible use of design and print analogies. If we overdo a packaging box with multiple forms of materials, it will not increase its visual beauty. On the other hand, it will make a mix-up and mumbo jumbo of colours. This is why retailers always demand an absolute design for their custom packaging.
-
The Importance of Product Design
Product design comes first when we talk about personalised packaging. Usually, the designer leads the packaging procedures. A designer sets the tone for the rest of the packaging product. He/she lays the foundation stone of the printing plates, colours, shades, and then the packaging style.
We can understand it with a simple example of printing on cardboard and Kraft materials. As I have stated above, brown is the default colour of Kraft. The brown colour does not comply with all the natural colours. Natural colours are also known as four offset colours.
These four offset colours are known as cyan (blue), magenta (a mix-up of blue and red), yellow, and black. When packaging companies print these four colours one after another, we get the real-life printed images. A problem occurs when people search for custom packaging: the brown colour of Kraft cannot bring the real cyan and magenta colours to its surface.
Brown currently has an effect on the natural tones of blue and magenta. As a result, we cannot have true picture quality on this surface. But a thinking designer can come up with some amazing duotone design themes.
The duotone design phenomenon comes with the merging of two contrasting colours. Duo means two or double. And when we talk on a whole, duotone means double tone colours. Designers should guide people towards its pleasant use while using Kraft.
A few examples include the colours blue and black, red and yellow, and green and red. Using two or more than two colours on Kraft can make a sensational packaging product. So, Kraft never disappoints you. There is only one condition; get a thinking designer.
-
How Does Printing Play its Part?
If you contact a packaging company to have some splendid packaging products, then printing is indispensable. Its first type is called offset lithography. It is famous by the name of offset printing. There was a time when people used to think that only digital printers could bring digital quality to paper.
They were correct in many ways. As we know, those digital printers were famous for photo printing. Many of us have experienced. Or, if you ask an expert in digital photography, he/she will tell you that, initially, digital printers were famous for personal photographs.
People have been looking for better ways of custom packaging since ages. Goldsmith Johannes Gutenberg invented the movable printing machine in 1440. This was the start of the printing revolution. It is well known in public that Gutenberg’s machine was capable of printing 3600 pages in a single day. This was a splendid result, keeping in mind the older print techniques.
This method was not only fast, but it also reduced the cost of printing to a great extent. This was a leap towards knowledge. Publishers printed the books in huge numbers. Businesses also entered a new sphere. Promotional and packaging products saw a new horizon.
Modern printing equipment is the apex of Gutenberg’s vision. Heidelberg is the most famous brand of offset printing machines. This German company is renowned for making single and multi-colour printing machines. Ironically, this is the same country where the first modern printing machine came into being.
KBA, KOMORI, MANROLAND, and RYOBI are also among the famous makers of printing equipment. These companies manufacture printing machines for both the corporate and private sectors. These machines give the optimum digital results in bulk quantities. Now we don’t need digital printers anymore to have the digital results on paper stocks.
-
How Does Paper/Paper Board Stocks Get Printed?
It would be handy if I write about the mechanism of these printing machines. It all starts with a single-colour machine. And then come to the plates. Usually, packaging companies use plates made of aluminium to attach to the plate cylinders. These are in the form of thin flat sheets. Machine men fix these plates on the cylinders. Thus, the plate becomes a part of the cylinder. These plates contain the printable (images) and non-printable areas on them. Actually, this is the product design that gets imprinted on the plates through a technical procedure.
If we ask professionals, they inform us that the offset printing machine works on the principle of oil and water division. Machine handlers put the ink into the machine. There are rubber rollers in the machine that get and pass the ink to the plate. The printable area (images and text, etc.) on the plate attracts the ink.
There is also a mini water tank attached to the printing machine. It prevents the ink from being laid on the non-printable area of the plate. Then a paper puller mechanism pulls the paper through the cylinders from the paper tray. When this paper gets rolled through the printing plate cylinder, it gets printed. A paper picker rod grabs the paper and takes it out of the cylinders. Thus, we get papers/cards printed.
Screen printing is the second most famous form of printing. It is also known as "silk screening", "silk screen printing", and "serigraphy". Initially, silk was used in this process. But nowadays, packaging companies use a sheet of synthetic thread to print it. Companies bring the design on the synthetic sheet and fix it in a wooden frame.
The design appears as a pattern on the sheet. Then they spread the colour on this sheet. Paperboard or stickers are laid under the sheet. A reverse stroke presses the screen to the paper surface. Hence, paper products get the ink through synthetic material. We can print one colour at a single time. This technique is ideal for printing Kraft material.
Block printing is another form of printing for the people who scroll for custom packaging. Some people who used to search for custom packaging Read a detailed blog about almost everything people search for custom packaging of products. Ask an expert at OXO Packaging to know more about new traits.say that it is the oldest form of printing. It has existed for thousands of years. We have found the evidence back in the fifth century BC.
This form of printing has roots in China, Japan, and India. It is a carved material. They prepare the engraved text and images in wood, linoleum, rubber, and many other materials. But wooden blocks are the most famous ones. They apply the ink on these blocks and then press them on the paper board surface. Hence, we get the printed image on the surface. Usually, this method adds a luxe touch to the packaging products.
What is embossing and debossing? It is our next level of learning. To do this process, packaging companies first make a die. We can also understand it as a block. It is a personalised metal plate. It is cut according to the images and text of your product design. The die presses and pressurises the surface of the stock.
Hence, it engraves the image or text on the surface. Two types of dies are in use. One is single-level and the second is multi-level. A single level raises the images to a consistent height or depth. whereas multi-level creates a complex emboss. Usually, people like to emboss their company logos, product names, or different patterns.
Similarly, the process of debossing works. But it has a different reverse technique than embossing. It has the same die. It creates a depressed effect on the images, logos, and text. If you are in search for custom packaging with luxury effects, then embossing and debossing are there for you.
It is evident that many times we see a simple one or two-colour packaging product. But packaging companies emboss or deboss the product name or logo. Only this method increases the visual appeal of the products. This is how people who search for custom packaging get amazing results each time.
-
The Future in Search for Custom Packaging
If you ask an expert in product packaging, what is the future of custom packaging? Then the professionals will inform you that paper-related packaging is changing rapidly. We have seen quick improvisations. Professionals say the last fifty years have been crucial.
The invention of new equipment has changed many things. The role of rigid set-up boxes has been reduced. Cardboard packaging boxes have come into the scenario. New packaging inventions by industrial scientists are opening new doors for people.
There was a time when lamination was the ultimate adoring choice for packaging products. Gloss and matte lamination were not only making products more presentable, but they were also making them waterproof to a greater extent. Then we saw a new breed, "soft touch lamination".
It is the next level. Conventional lamination was not much scratch-proof. But this new improvisation is much thicker and makes the lamination more scratch-proof. This all happened when we still have not fully consumed the spot UV effects.
Similarly, materials are getting better and better with more features. The foil material is a luminating example. People who used to look for custom packaging with foil printing have got a new sensation. Holographic foil has changed many things. It is a simple foil but with multi-colours.
The eco-friendly aspect of packaging is another growing factor of custom printed paper product packaging because you can dispose of the packaging after use. And then the paper mill recycles the stock. So, paper-related packaging is here to stay. And we will depend on it even more. Hope this blog helped you to learn more about custom product packaging. If you have anything to say, catch me in the comments.